Use of approved codes of practice to ensure compliance
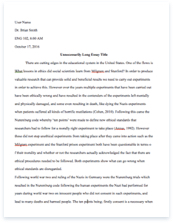
- Pages: 20
- Word count: 4821
- Category: Construction
A limited time offer! Get a custom sample essay written according to your requirements urgent 3h delivery guaranteed
Order Now
The Approved Codes of Practice (ACOP) is a practical guide to achieving the standards of health, safety and welfare required. A code of practice applies to anyone who has a duty of care in the circumstances described in the code. In most cases, following an approved code of practice would achieve compliance with the health and safety duties , in relation to the subject matter of the code. Like regulations, codes of practice deal with particular issues and do not cover all hazards or risks that may arise. The health and safety duties require duty holders to consider all risks associated with work, not only those for which regulations and codes of practice exist.
The ACOP has special legal status and gives practical advice for all those involved in construction work. If we follow the advice in the Approved Codes of Practices, we will be doing enough to comply with the law in respect of those specific matters on which it gives advice. Also ACOP offer practical examples of good practice. They give advice on how to comply with the law by, for example, providing a guide to what is âreasonably practicableâ.
The ACOP explains:
The legal duties placed on clients, Construction Design and Management (CDM) co-ordinators, designers, principal contractors, contractors, self-employed and workers. The circumstances in which domestic clients do not have duties under CDM 2007 (but that the regulations still apply to those doing work for them). Gives information on the new role of CDM co-ordinator â a key project adviser for clients and responsible for coordinating the arrangements for health and safety during the planning phase of larger and more complex projects.
Which construction projects need to be notified to HSE before work starts and gives information on how this should be done. How to assess the competence of organisations and individuals involved in construction work. How to improve co-operation and co-ordination between all those involved in the construction project and with the workforce. What essential information needs to be recorded in construction health and safety plans and files, as well as what shouldn’t be included.
For example, if regulations use words like âsuitable and sufficientâ, an Approved Code of Practice can illustrate what this requires in particular circumstances. Approved Codes of Practice have a special legal status. If employers are prosecuted for a breach of health and safety law, and it is proved that they have not followed the relevant provisions of the Approved Code of Practice, a court can find them at fault unless they can show that they have complied with the law in some other way. In providing guidance, the word âshouldâ is used in this Code to indicate a recommended course of action, while âmayâ is used to indicate an optional course of action.
Health and Safety Commission (HSC), consulted in 1995 on the role of Approved Codes of Practice in the health and safety system and concluded that they could still be used in support of legal duties in specific circumstances.
Regulations are law, approved by Parliament. These are usually made under the Health and Safety at Work Art, following proposals from HSC. This applies to regulations based on EC Directives as well as âhome-grownâ ones. The Health and Safety at Work Art, and general duties in the Management Regulations, are goal setting and leave employers freedom to decide how to control risks which they identify. Guidance and Approved Codes of Practice give advice.
But some risks are so great, or the proper control measures so costly, that it would not be appropriate to leave employers discretion in deciding what to do about them. Regulations identify these risks and set out specific action that must be taken. Often these requirements are absolute to do something without qualification by whether it is reasonably practicable.
All parties to a contract have specific responsibilities under health and safety law, and these cannot be passed on to someone else: employers are responsible for protecting people from harm caused by work activities. This includes the responsibility not to harm contractors and sub-contractors on site employees and contractors have to take care not to endanger themselves, their colleagues or others affected by their work contractors also have to comply with the HSW Act and other health and safety legislation.
Clearly, when contractors are engaged, the activities of different employers do interact. So cooperation and communication are needed to make sure all parties can meet their obligations employees have to cooperate with their employer on health and safety matters, and not do anything that puts them or others at risk employees must be trained and clearly instructed in their duties self-employed people must not put themselves in danger, or others who may be affected by what they do suppliers of chemicals, machinery and equipment have to make sure their products or imports are safe, and provide information on this.
The Management of Health and Safety at Work Regulations apply to everyone at work and encourage employers to take a more systematic approach to dealing with health and safety by:
- assessing the risks which affect employees and anyone who might be affected by the site occupierâs work, including contractors setting up emergency procedures
providing training
cooperating with others on health and safety matters, for example, contractors who share the site with an occupier providing temporary workers, such as contractors, with health and safety information
For the Client, they are those involved in a trade, business or other undertaking (whether for profit or not) and for whom construction work is carried out. Domestic clients are a special case and do not have duties under CDM.
For the designers, they are the organizations or individuals who carry out the design of the project. Designers may include architects, consulting engineers, quantity surveyors, specifiers, principal contractors and specialist sub-contractors.
For planning supervisor, it can be a company, partnership, organization or an individual who coordinates and manages the health and safety aspects of the design. The planning supervisor also has to ensure that the pre-tender stage of the health and safety plan and the health and safety file are prepared. The Regulations suggest that the planning supervisor will normally be more than one person, except for the smallest of projects.
For Principal contractor, this is the contractor appointed by the client who has overall responsibility for the management of the site operations. This includes the overall coordination of site health and safety management.
For the Health and safety plan, there are in effect two health and safety plans: the pre-tender health and safety plan prepared before the tendering process brings together the health and safety information obtained from the client and designers and aids selection of the principal contractor and the construction stage health and safety plan details how the construction work will be managed to ensure health and safety
For the Health and safety file, this is a record of information for the client which focuses on health and safety. It alerts those who are responsible for the structure and equipment in it to the significant health and safety risks that will need to be dealt with during subsequent use, construction, maintenance, repair, cleaning and demolition.
Lastly, it is the Method statement, this is a written document laying out the work procedures and sequences of operations to ensure health and safety. It results from the risk assessment carried out for the task or operation and the control measures identified. If the risk is low, a verbal statement may suffice.
2. Explaining the responsibilities for providing welfare facilities on-site (P1.2)
The Health and Safety Executive have been concerned for some time at the poor standard of welfare facilities on many construction sites. Welfare arrangements include the provision of sanitary conveniences and washing facilities, drinking water, accommodation for clothing, facilities for changing clothing and facilities for rest and eating meals.
Sanitary and washing facilities (including showers if necessary) with an adequate supply of drinking water should be provided for everybody working on the site. Accommodation will be required for the changing and storage of clothes and rest facilities for break times. There should be adequate first-aid provision (an accident book) and protective clothing against adverse weather conditions. Welfare issues are covered by the Construction (Health, Safety and Welfare) Regulations 1996. Information is also available in the Approved Codes of Practice and additional guidance for the Workplace (Health, Safety and Welfare) Regulations 1992.
Sanitary conveniences and washing facilities must be provided together and in a proportion to the size of the workforce. The Approved Code of Practice of the Workplace (Health, Safety and Welfare) Regulations 1992 provides two tables offering guidance on the requisite number of water closets, wash stations and urinals for varying sizes of workforce (approximately one of each for every 25 employees). Special provision should be made for disabled workers and there should normally be separate facilities for men and women.
There should be adequate protection from the weather and only as a last resort should public conveniences be used. A good supply of warm water, soap and towels must be provided as close to the sanitary facilities as possible. Hand dryers are permitted but there are concerns about their effectiveness in drying hands completely and thus removing all bacteria. In the case of temporary or remote work sites, sufficient chemical closets and sufficient washing water in containers must be provided. All such facilities should be well ventilated and lit and cleaned regularly.
Drinking water must be readily accessible to all the workforce. The supply of drinking water must be adequate and wholesome. Normally mains water is used and should be marked as âdrinking waterâ if water not fit for drinking is also available. On some sites, particularly during the early stages of construction, it may be necessary to provide bottled water or water in tanks. In this event, the water should be changed regularly and protected from contamination. Cups or mugs should be available near the tap unless a drinking fountain is provided.
Accommodation for clothing and facilities for changing clothing must be provided which is clean, warm, dry, well-ventilated and secure. Where workers are required to wear special or protective clothing, arrangements should be such that the workersâ own clothing is not contaminated by any hazardous substances. On smaller sites, the site office may be suitable for the storage of clothing provided that it can be kept secure and used as a rest facility.
Facilities for rest and eating meals must be provided so that workers may sit down during break times in areas where they do not need to wear personal protective equipment. It should be possible for workers to make hot drinks and prepare food. Separate rooms should be provided for smokers and non-smokers. Facilities should also be provided for pregnant women and nursing mothers to rest. Arrangements must be in place to ensure that food is not contaminated by hazardous substances. Many fires have been caused by placing clothes on an electric heater. Damp clothes should not be positioned in contact with the heater and there should be adequate ventilation around the heater. If possible, the heater should be fitted with a high temperature cut-out device.
The location of the welfare facilities on the site is important. They should be located adjacent to each other and as close to the main working area as possible. It is likely that as the work progresses, the welfare facilities will need to be moved. It may be appropriate to use facilities in neighbouring premises. However, all such arrangements must be agreed in advance with the relevant neighbour. Reliance on public conveniences should be avoided due to their unreliability and lack of hot water for washing.
Welfare arrangements for transient sites will be different to those for fixed sites. Transient sites include sites where the construction work is of short duration (up to one week in many cases), such as road works and emergency work. In these cases, welfare facilities (toilets, hand-washing basins, rest and eating arrangements) may be provided by a suitably equipped vehicle or by siting fixed installations at intervals along the length of the job.
For general duties, it can be placed on several groups. For examples, employers, employees, self-employed, manufacturers (including designers, importers and suppliers) and people who control work promises.
For employers duties, they must ensure the safety, health and welfare of all their employees if so far as is reasonably practicable. This is often referred to as the âGeneral duty of employers to their employeesâ and is the greatest and most influential part of all the safety laws. They need to pay great effort to put into making sure something is safe. It places safety securely in the position of first priority.
For specific duties, it goes on to expand on these and gives 5 categories of particular things that employers must do, so far as is reasonably practicable. These are:
1. Plant and systems of work
To provide and maintain plant (equipment) and systems of work (practices) that are safe and without risks to health;
2. Use, handling, storage and transport
To ensure that the use, handling, storage and transport of articles (things) and substances (chemicals and materials) are safe and without risks to health;
3. Information
To ensure that employees have the information, instruction, training and supervision they need to be safe;
4. Access and egress
To ensure that the workplace itself is safe and that there are safe ways to get to it and away from it â including in an emergency;
5. Environment and welfare
To provide and maintain a working environment that is safe, free from health risks and has adequate welfare facilities.
For other duties of employers, duty to ensure the safety of all others not in their employ, but who may be affected by the work such as public, visitors, subcontractors and children.
For others with duties, Sub-contractors have the same responsibilities as main employer. The Self employed have duties to care for themselves and ensure that their activities do not affect the safety and health of others. The employeesâ act also puts a duty on all employees to take care for themselves, not to endanger others, not to tamper with safety equipment, and to assist employers in carrying out their duties under the Act. The designers, manufacturers, suppliers, importers of any article or substance must ensure that it will not endanger users. The Construction Design and Management Regulations made under this Act, now give much more detail about building designersâ duties. The landlords and building owners anyone who provides a building, or land, for use as a workplace must make sure that it is safe and suitable for the intended use, and that there are safe routes of entry and escape.
For more, the Clients and contractors have responsibilities regarding welfare facilities on construction projects. Contractors provide welfare facilities and clients must ensure this happens.
The pre-construction information prepared by the client should include the arrangements for welfare provision. On notifiable projects (longer than 30 days or 500 person days), the client must ensure the construction phase does not start unless they are satisfied that there are arrangements for welfare facilities to be provided.
If mobile teams work at a number of locations over a few days (e.g. road repair and cable-laying gangs), these facilities can be provided at a central location accessible within a reasonable distance or time. Decisions and action on welfare facilities need to be taken at an early stage of project planning.
The Act puts responsibilities upon all parties at work to protect themselves, those they employ, and those they work with. When we add the responsibility to protect the general public, we can see that the Act has a very broad scope, with many duties and responsibilities being placed upon all parties involved in a work operation.
3. Explaining the Construction (Design and Management) Regulations 2007. Evaluate the penalties for non-compliance with current health and safety at work legislation. Give at least two examples for easy understanding. (P1.3)
The Construction (Design and Management) Regulations 2007, also known as CDM Regulations or CDM 2007, define legal duties for the safe operation of UK construction sites. The regulations place specific duties on clients, designers and contractors, to plan their approach to health and safety. They apply throughout the life of a construction project, from its inception to its subsequent final demolition and removal. It was introduced by the Health and Safety Executive’s Construction Division to help:
Improve planning and management of projects from the very start of the project; Identify hazards early on so they can be eliminated or reduced at the design or Planning stage, and then the remaining risks can be properly managed; Target effort where it can do most good in terms of health and safety; Discourage unnecessary bureaucracy.
Assign the right people for the right job at the right time to manage the risks on site;
The aim is for health and safety considerations to be treated as an essential, but normal part of a projectâs development â not an afterthought or bolt-on extra.
The layout of the Regulations are divided into 5 parts:
Part 1 – interpretation and application of the regulations. Legal definitions of what certain terms mean, and how the Regulations apply. Part 2 – general management duties which apply to all construction projects no matter how big or small. Part 3 – additional management duties which apply to projects above the notification threshold. These additional duties require particular appointments or particular documents which will assist with the management of health and safety from concept to completion. Part 4 â covers physical safeguards which need to be provided to prevent danger, and applies to all work on construction sites. Duties to ensure safety are owned by any party who has control over that work, and in the proportion to which they have that control, i.e. the more control you have over the work, the higher your duty of care. Part 5 – covers issues of civil liability, transitional provisions that apply during the period when the regulations come into force, and amendments and revocations of other legislation.
CDM 2007 applies to all construction work and covers a very broad range of construction activities such as building, civil engineering, engineering construction work, demolition, site preparation and site clearance, except for which only applies if the project is notifiable.
On a notifiable project, the client must additionally appoint a competent CDM co-ordinator and a competent Principal Contractor, a Construction Phase Plan ( âConstruction Phaseâ â incorporating Mobilisation (let the building contract, appoint contractor, issue production information, arrange site hand-over, and review contractorâs proposals), Construction to Practical Completion (administer the building contract and provide contractor with further information as necessary), After Practical Completion (administer the building contract after practical completion, resolve defects and make final inspections).
The importance of this phase is in the inspection of expected performance standards to ensure compliance).and a Health & Safety File must be produced. Additional duties are also placed on the Client, Designers and Contractors for notifiable projects. The CDM Co-ordinator is the new title for the Planning Supervisor under CDM 1994, with increased duties and responsibilities.
For the penalties for non-compliance with current health and safety at work legislation, there are some examples:
Personal protective equipment (PPE) is an important means of preventing work injuries. Ideally, the best approach is to maintain a safe work environment and eliminate any potential hazards. PPE should only be relied upon as a last line of defence in places where it is not practicable to control the hazards at source.
The use of PPE generally implies working in a potentially hazardous work environment and its use is a major means of injury prevention. Therefore, it is of prime importance to ensure that the equipment chosen is both reliable and effective, it is being properly used and maintained, and the user has undergone adequate training. The aim of this booklet is to raise the awareness of occupational safety and health practices and the proper use of PPE of people from all walks of life
The “Construction Sites (Safety) Regulations” clearly state that no person shall enter a construction site without wearing a suitable safety helmet. In other places where there is the risk of falling objects, workers must also correctly wear safety helmets to avoid head injury
Also, fall from height accidents could cause serious injuries. Employers and employees engaged in work at height should pay particular attention to the hazards involved and adopt adequate precautions. To ensure the safety and health of the workers in work at height, the Council has launched the âAnchor Device Sponsorship Scheme for Renovation & Maintenance SMEsâ and âSafe Ladder Sponsorship Scheme for SMEsâ. The schemes assist the employers of small and medium enterprises involved in work at height. The sponsorship goes to the purchase of anchor devices for fall protection system and safe ladders.
From the Legislation and Code of Practice of Occupational Safety and Health Regulation – Section 6, A person responsible for a workplace who fails, without reasonable excuse, to comply with a platform, pit or opening located within a workplace could be a danger to the safety of persons, the person responsible for the workplace must ensure that the platform, pit or opening is securely fenced to a height of 900 mm (measured from the upper surface of the platform, or of the edge of the pit or opening) commits an offence and is liable on conviction to a fine of $200000.
4. Analyse organizational health and safety policies and procedural documents (P2.1)
There are 5 key elements to managing the workplace in a healthy and safe way suggested from the HSE publication âSuccessful Health & Safety Managementâ
The main elements as set out in the above Figure are discussed in detail in the following paragraphs.
Policy
A good health and safety policy can contribute to business performance by: Supporting human resource development;
Minimizing financial losses from avoidable unplanned events; Recognizing that accidents and ill health can result from management failures, as well as in employee faults; Recognizing that a supportive culture is required to achieve adequate control of risks; Ensuring a systematic approach to the identification of risks and the allocation of resources to control them;
Effective health & safety management demands comprehensive health and safety policies which:
Fulfill the spirit and the letter of the law;
Are effectively implemented;
Are considered in all business practice and decision making.
Organisations achieving high standards of health and safety develop policies which recongnise: Health and safety can contribute tot business performance by preserving and developing human and physical resources, by reducing costs and liabilities and as means of expressing corporate responsibility. Leaders must develop appropriate organizational structures and a culture which supports risk control and secures the full participation of all members of the organization.
The main components of the written safety policy should be including:
The policy statement
This should give a clear statement of the companyâs commitment to health and safety, should be seen as a document with authority and signed by the director responsible for safety, state when policy will be upgraded, state how safety is to be monitored outline consultation methods with safety representatives.
The Organisation
The policy should state the duties of individuals who has final responsibility for safety.
The Arrangements
The policy should contain details of arrangement for training, safe systems of work, environmental control and safe place of work,etc.
Typical organizational management chain of responsibilities for safety:
Organising
It is securing CONTROL by managers who lead by example:
Clear allocation of responsibilities
Ensuring that individuals are held responsible for their health and safety responsibilities and ar Also, it is encouraging CO-OPERATION of employees and safety representatives.
Planning & Implementation
Organisation achieving success in health and safety minimize risk in their operation by drawing up plans and setting performance standards with the aim to eliminate and control risks. Identify objective and targets for their achievement within a specific period; Set performance standards for management;
Eliminate risks by substitution of safer methods of work and use of safer materials; Ensure the adequate documentation of all performance standards
Measuring Performance
Active systems monitor the achievement of plans and the extent of compliance with standards.
Active monitoring provides the feedback before the accident or ill-health occurs.
Also, the reactive systems monitor accidents, ill health and safety. Active monitoring provides the feedback after the accident or ill-health occurs typically these systems collect and analyse information suggesting failures in safety performance, such as injuries and cases of ill health, loss events ie demage to property.
Reviewing performance and auditing
Learning from experience through the use of audits and performance reviews enables organizations achieving high standards of health and safety to maintain and develop their ability to manage risks to the fullest possible extent.
The aim of this review is to make the maximum use of knowledge gained from experience in order that health and safety standards can be improved.
5. Determine training needs from given risk assessments, including on-site induction training and relevant sector certification. Give at least one example to illustrate training needs (P2.2)
There are some key elements of a suitable and sufficient risk assessment. For example: Worker involvement
A hazard identification process (which will entail data gathering and analysis) Gap analysis
Solution development
HSE and Local Authority inspectors also recommend following the Management Standards to assess the risks of work related stress in organization.
Also, the construction industry is now moving towards a system where everybody working in the industry will have to have proof of his or her competence. This will be done through a registration scheme such as the Construction Skills Certification Scheme (CSCS). CSCS will issue Experienced
Workers Cards to construction workers to indicate their level of ability, based on their employerâs endorsement.
CSCS aims to register every competent construction operative within the UK not currently on a skills registration scheme. Operatives will get an individual registration card (similar to a credit card) which lasts for three or five years. The CSCS card also provides evidence that the holder has undergone health and safety awareness training or testing.
CSCS cards provide a consistent method to check construction workersâ competency before allowing them access to sites. Most major contractors require their workers to hold a valid CSCS card as demonstration of their commitment to safe and efficient working.
To illustrate training needs, everyone who works for we needs to know how to work safely and without risks to health. Employer must provide clear instructions, information and adequate for the employees. Contractors and self-employed people who may be working and make sure everyone has information on hazards and risks they may face, measures in place to deal with those hazards and risks and how to follow any emergency procedures.
Employees should make sure the training is relevant and effective. Keeping the training records will help to identify when refresher training might be needed. The information and training we provide should be in a form that is easy to understand. Everyone should know what they are expected to do.
Health and safety training should take place during working hours and it must not be paid for by employees. There are many external trainers who will be able to help with training needs but effective training can often be done âin houseâ.
There are some employees may have particular training needs. For examples:
New recruits need basic induction training into how to work safely, including arrangements for first aid, fire and evacuation; People changing jobs or taking on extra responsibilities need to know about any new health and safety implications; Young employees are particularly vulnerable to accidents and you need to pay particular attention to their needs, so their training should be a priority. It is also important that new, inexperienced or young employees are adequately supervised; Some peopleâs skills may need updating by refresher training. Employee representatives or safety representatives will require training that reflects their responsibilities.
Also, there are some specialist courses for people to take:
The ever changing nature of construction operations e.g. new materials, new construction methods, new plant and equipment, together with the regular addition of new legislation requires staff to be re-trained and brought up-to-date with safety needs.
The use of specialist short courses is often the most appropriate method of implementing such training. The following are short courses may need to be used: Small plant and equipment;
Transport;
Excavation;
New legislation
In conclusion, the risk assessment should identify any further training needs associated with specific risks for the construction site.
Reference:
http://www.hse.gov.uk/construction/cdm/acop.htm
Notes
http://en.wikipedia.org/wiki/Construction_(Design_and_Management)
http://www.airforce.gov.au/docs/vol2/VOLUME2%20Part2.htm